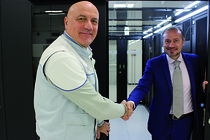
Lo stabilimento Sevel (Società Europea
Veicoli Leggeri) di Atessa, in provincia di
Chieti, è il più grande impianto mondiale
per la produzione di veicoli commerciali leggeri,
ovvero i furgoni utilizzati per gli impieghi
più disparati. Benché le linee siano attive 320
giorni all’anno e realizzino circa 300 mila veicoli
ogni anno, la produzione non è sufficiente
a soddisfare una domanda che, per l’85%, è
esportata fuori dall’Italia. Così, pur a fronte di
una produzione quotidiana di 1.200 veicoli, i
responsabili aziendali sono alla continua ricerca
di soluzioni per massimizzare efficienza e produttività.
Ogni cliente ha esigenze specifiche,
dettate dal proprio lavoro, dal materiale che
deve essere caricato o dalle condizioni ambientali
in cui opererà. L’impianto di Sevel è così in
grado di realizzare oltre 17.000 diverse versioni
e, quindi, di soddisfare qualunque necessità.
Dall’ordine alla messa
in strada
In pratica, non appena viene sottoscritto un ordine
di acquisto in qualunque concessionaria
europea, i dati e le specifiche tecniche sono inseriti
nel gestionale aziendale. Uno strumento
informatico in grado di definire le forniture di
materie prime necessarie e di pianificare l’ordine
di produzione. Tutte le informazioni necessarie
arrivano anche alle linee produttive, dove
vengono assemblati, a distanza di pochi minuti,
versioni ed equipaggiamenti completamente
diversi, ognuno dei quali è tracciato e monitorato
nell’intero percorso in uno stabilimento in
cui lavorano oltre 6.000 persone. Tutto questo
non può avvenire senza il supporto delle soluzioni
informatiche più innovative, chiamate
a funzionare sempre, fornendo le indicazioni
logistiche e di montaggio a tutti i soggetti coinvolti
nell’assemblaggio dei veicoli. Proprio l’Ict,
negli ultimi anni, è stato chiamato a sfide sempre
più impegnative, per rispondere alle esigenze
di una maggiore produttività e per fare fronte
al crescente numero di dati da raccogliere e gestire
in locale. Il Cloud, infatti, non rappresenta
sempre la soluzione ideale, in quanto i tempi di
latenza sono eccessivi rispetto alle esigenze produttive.
Da qui la necessità di concentrare ad
Atessa l’enorme mole di dati necessari alla produzione,
inviando al Data Center centrale del
Gruppo solo i report generali. L’elaborazione
vera e propria, quindi, deve rimanere vicina al
punto di produzione dei dati stessi e di utilizzo
delle informazioni, seguendo la logica dell’Edge
Computing. Garantire la continuità operativa,
però, non è semplice. L’intero impianto può essere
messo in crisi dalle situazioni più svariate e
inattese, come accaduto nel 2017, poco dopo la
nevicata che ha investito il Centro Italia. Lo stabilimento
di Atessa è stato colpito da una serie
di blackout, alcuni dei quali si sono prolungati
per 10 ore: questo ha bloccato la produzione,
ma non il Data Center dove, grazie alla dotazione
di Ups sovradimensionati, il reparto Ict
è rimasto sempre operativo ed ha proseguito la
propria attività.
Due Data Center speculari
La creazione del nuovo Data Center è stata
affidata da FCA a N&C Telecomunicazioni,
l’azienda che fornisce al Gruppo il servizio di
SPOC per le componenti di Networking, Security,
Voice, PC Desktop, Server e Infrastrutture
Data Center. La scelta è stata quella di realizzare
in Sevel due Data Center fisicamente distanti
tra loro, ma speculari e ridondati a caldo,
con gli UPS segregati in locali chiusi da pareti e
porte a prova di incendio. Accanto alla componentistica
elettrica, tradizionale punto di forza
di Legrand, attraverso la competenza BTicino,
l’azienda oggi propone un’offerta completa, che
va dai rack ai sistemi di condizionamento, passando
attraverso il monitoraggio e le soluzioni
di cablaggio strutturato. Del resto, in una fabbrica
ispirata ai più moderni criteri di Industria
4.0, l’intera produzione è guidata dall’informatica,
che assume un ruolo determinante e non
può prescindere dalle eccellenze di mercato.
L’alimentazione e la protezione delle apparecchiature
elettroniche rivestono così un’importanza
altrettanto fondamentale.
L’idea è stata di creare due Data Center speculari,
con carichi bilanciati in grado di garantite
il corretto funzionamento delle linee produttive
anche in caso di fault di uno dei due. Un obiettivo
raggiunto rispettando tutti i requisiti tecnici
che caratterizzato i Ced con il più elevato
livello di affidabilità oggi possibile.
L’isola Legrand Data Center
In un Data Center chiamato a ospitare un’elevata
concentrazione di server, il primo aspetto da
considerare è il raffrescamento delle apparecchiature
ospitate. La produzione di calore, che
deve essere smaltito, è infatti proporzionale alla
potenza elettrica assorbita del singolo elaboratore.
Due aspetti particolarmente elevati nello
stabilimento di Atessa. Gli uffici progettazione
di FCA e N&C Telecomunicazioni hanno così
scelto di sfruttare la tecnologia delle isole “Next
Generation Cold Corridor”, di Legrand LDCS,
divisione del Gruppo Legrand specializzata nella
realizzazione di Data Center. Una soluzione
che permette la netta separazione del corridoio
caldo/freddo, cioè l’aria calda di scarico dei server
viene racchiusa in un plenum, dove viene
rapidamente rimossa e raffrescata dai condizionatori
infra-rack “Varicondition-DX”. Confinare
il corridoio caldo/freddo in zone distinte, se
da una parte permette la completa separazione
del caldo dal freddo, dall’altro permette di massimizzare
l’efficienza energetica dei condizionatori
in quanto riprenderanno sempre e solo aria
ad alta temperatura. Dalla parte opposta dell’isola
avremo il corridoio freddo che, a temperatura
costante di 23-25°C raffrescherà l’infrastruttura
all’interno della quale sono racchiuse
le apparecchiature informatiche. Grazie a questa
particolare isola, inoltre, i tecnici di Sevel
operano direttamente sugli apparati dall’esterno
del “corridoio freddo” e, quindi, in condizioni
ambientali ideali per svolgere le proprie attività.
Il risultato più emblematico della corretta
scelta impiantistica, è stato misurato già poche
settimane dopo l’entrata in funzione del nuovo
Data Center. Il PUE (Power Usage Effectiveness
– ovvero il rapporto tra la potenza assorbita e
quella effettivamente utilizzata dalle apparecchiature
informatiche) è pari 1,3. Un valore tra
i più bassi oggi raggiungibili, soprattutto in una
regione d’Italia caratterizzata da alte temperature
ambientali. É questa la conferma dell’elevata
efficienza energetica dell’intero Data Center,
che sfrutta al meglio i moduli di refrigerazione
ad “espansione diretta” Legrand Varicondition,
equipaggiati con compressori inverter del tipo
“Twin Rotary”, con alto coefficiente di efficienza
ed integrati nelle file di armadi.
Affidabilità senza compromessi
Affidabilità e continuità operativa sono infatti
l’ossessione per chiunque debba gestire grandi
moli di dati a servizio di un impianto produttivo.
L’attenzione, quindi, non può prescindere
dall’affidabilità e dalla continuità di alimentazione.
Anche il Data Center più performante,
infatti, può essere messo in crisi da un banale
problema elettrico. Un’eventualità che Sevel
non può tollerare, poiché comporterebbe l’immediata
interruzione della produzione. Gli specialisti
di N&C Telecomunicazioni, hanno così
sviluppato una soluzione caratterizzata dalla
ridondanza 2N di ogni singolo elemento ma,
soprattutto, da un controllo minuzioso e tempestivo
dei valori elettrici e ambientali. Da qui
anche l’impiego dei quadri elettrici Infra-rack
Legrand dotati del sistema “TiFast di BTicino”,
con aggancio e sgancio a caldo dei singoli magnetotermici.
Questa soluzione, come spiega
Gianluca Giannuzzi di N&C Telecomunicazioni,
ci ha permesso “di completare rapidamente
l’installazione, realizzando facilmente cablaggi
elettrici anche molto complessi in spazi ridotti”.
La famiglia di prodotti, infatti, propone soluzioni
pronte all’uso per il collegamento in ingresso
e in uscita degli interruttori fino a 400A
per ognuna delle due linee d’alimentazione. In
questo modo è stato possibile realizzare armadi
elettrici nei quali le attività di ampliamento e
manutenzione risultano semplificate e possono
essere completate, in sicurezza, anche all’interno
di rack sotto tensione. Un aspetto fondamentale
di un Data Center chiamato a supportare
linee produttive in funzione, su più turni,
per 320 giorni all’anno. Oltre alla ridondanza, i
tecnici ICT richiedono di essere costantemente
informati sullo stato di ogni singolo parametro,
per poter intervenire in modo proattivo. Da
qui la scelta di integrare le PDU PX3 di Raritan
(altro brand del Gruppo Legrand). Queste
innovative unità di distribuzione di potenza
rilevano, in tempo reale, sia i carichi elettrici
collegati che le variabili microambienti, come
temperatura e umidità, presenza liquidi, o registrazione
tramite WEB-CAM, comunicandole
anche a distanza attraverso la rete di cablaggio
strutturato Ortronics (altra marca Legrand).
Grazie alle colorazioni dello chassis delle PDU,
distinte per UPS di provenienza (Rosse UPS A e
Nere UPS B), con le PDU intelligenti Raritan -
spiega De Nardis - siamo in grado di prevenire
eventuali errori umani, ma il principale valore è
dato dal sistema di monitoraggio, grazie al quale
individuiamo in anticipo eventuali problemi o
anomalie, intervenendo così in modo proattivo.
L’intero sistema è stato configurato per permettere,
ad ogni tecnico coinvolto, di ricevere solo gli
allarmi effettivamente significativi per il suo lavoro.”
E’ questo un ulteriore esempio dell’attenzione
riservata alla corretta gestione dei carichi
elettrici all’interno del Data Center dello stabilimento.
Un’attenzione che, unita alla ridondanza
dei circuiti elettrici, di quelli di raffreddamento e
di rete permette a SEVEL di fronteggiare anche
gravi incidenti tecnici, con una disponibilità dei
dati pari al 99.995%. Il tutto con un’attenzione
significativa anche al risparmio energetico.