Le proposte di automazione industriale offerte dalle aziende sono tecnologicamente diversificate. L’utilizzatore (Oem o System integrator) deve essere preparato per la scelta della soluzione da utilizzare, in particolare nelle applicazioni performanti per prestazioni, funzionalità e di sicurezza macchinario/impianto
I fornitori di automazione sono molto attivi e offrono consulenza per mezzo dei loro funzionari tecnici, i quali cercano di preparare tecnicamente i loro clienti. Scegliere una tecnologia a scapito di un’altra è comunque un’operazione molto complessa e delicata. La scelta del sistema di controllo è la principale decisione strategica nella fase iniziale di studio dell’automazione di una macchina o di un impianto industriale.
Analisi: PC industriali, PLC e PAC
Un controllore di automazione programmabile (PAC) è un controller compatto, che unisce le caratteristiche e le funzionalità di un PC basato su sistema di controllo con quella di un tipico controllore logico programmabile (PLC).I sistemi PAC sono più spesso utilizzati in ambienti industriali per il controllo di processo, acquisizione dati, apparecchiature di monitoraggio a distanza, visione artificiale e controllo del movimento. Inoltre, perché funzionano e comunicano con interfaccia di rete tramite protocolli quali TCP / IP, OLE for Process Control (OPC) e SMTP,i PAC sono in grado di trasferire i dati dalle macchine che controllano ad altre macchine. L’ARC Advisory Group, un gruppo analista focalizzato sul settore manifatturiero, è generalmente accreditato per avere creato il termine “PAC”. È stato coniato nel 2001 come un modo per aiutare gli utenti di hardware di controllo a definire meglio le loro esigenze, e di dare ai principali fornitori di hardware di controllo un termine per comunicare più chiaramente le potenzialità dei loro prodotti. In generale, PAC e PLC servono allo stesso scopo. Entrambi sono utilizzati principalmente per eseguire l’automazione, controllo di processo, e le funzioni di acquisizione dati, digitali e analogici di controllo, gestione delle stringhe di serie, PID, controllo del movimento, e la visione della macchina. I parametri entro i quali operano PAC per raggiungere questo obiettivo, tuttavia, sono a volte in contrasto con il funzionamento delle funzioni PLC. A differenza dei PLC, che costantemente attuano la scansione di tutti gli I/O nel sistema di controllo a velocità molto elevate, PAC utilizza un unico database tagname e un indirizzo logico di sistema per identificare e mappare i punti di I/O in base alle esigenze. I computer industriali invece rivestono un ruolo di primaria importanza sia a livello di area (workstation, potenti elaboratori…) sia a livello di cella (PC industriali o computer modulari per la realizzazione di sistemi di supervisione, controllo di processo, interfaccia operatore…). Sono dotati di elevato potere di calcolo, si interfacciano facilmente ad altri computer, con i quali possono condividere dati e programmi, consentono la gestione diretta di segnali anche non numerici, sono dotati di software di base che semplifica la programmazione e la gestione da parte dell’utente. Il computer si è evoluto dall’ambiente dell’ufficio all’area industriale grazie alla sua versatilità, semplicità d’uso e diffusione ed è stato adattato a questo nuovo ambito di lavoro rendendo più affidabile il software e più robusto l’hardware.
Elemento tecnologico importante: il software
Con il termine PAC (Programmable Automation Controller), si evidenziano dei controller compatti o modulari ibridi che combinano le caratteristiche e le capacità di un sistema di controllo basato su processore PC con quella di un tipico controller logico programmabile. I PLC (Programmable Logic Controller) sono strutturati come dei microcomputer industriali e sono utilizzati principalmente per eseguire l’automazione, il controllo dei processi e le funzioni di acquisizione dei dati, come il controllo real-time dei segnali digitali e analogici, la gestione di calcoli complessi su variabili e array, il controllo del movimento, la gestione dei Pid, la diagnostica, il controllo a distanza. Considerando la grande differenza tra i piccoli e i grandi PLC, i programmi possono essere molto semplici ma anche molto articolati e complessi. Spesso sono ampiamente supportati da software di base che permettono l’utilizzo di linguaggi con macrofunzioni, simbolici o simil-grafici. La differenza di base tra un PAC e un PLC è da analizzare per la componente software, che permette di avere a disposizione un linguaggio di programmazione grafico intuitivo, simile a uno schema di flusso, ma associato a sistemi operativi real-time e con possibilità di definizione di hardware riconfigurabile. I programmi di controllo sono in genere sviluppati con strumenti software generici che permettono di progettare il programma per essere condiviso tra più computer, processori, terminali Hmi o altri componenti dell’architettura del sistema di controllo. I PAC sono particolarmente adatti alle comunicazioni che sfruttano protocolli standard e interfacce di rete e sono solitamente racchiusi in contenitori non più grandi di quello di un comune PLC: in tale spazio trovano posto un microprocessore evoluto, svariati moduli di memoria (sia volatile che permanente), moduli di controllo assi e diversi modelli d’interfaccia di comunicazione. L’intelligenza di bordo è fornita dai tools di un sistema operativo, tipicamente in tempo reale in grado di offrire bassi tempi di latenza e un determinismo adatto all’impiego in compiti critici, e da un software applicativo evoluto che è solitamente realizzato su piattaforme di sviluppo di tipo PC e successivamente “scaricato” nel dispositivo. Nel panorama odierno tutti i principali fornitori di automazione propongono entrambe le soluzioni, e la tendenza generale è comunque quella di chiamare PLC un sistema che ha le caratteristiche prestazionali di PAC.
Alcune tappe dell’evoluzione tecnologica
I PLC hanno sempre contribuito ai progressi nel campo del controllo delle macchine automatiche, dai piccoli controlli usati nelle macchine operative, ai controlli su ampia scala destinati al comando di complessi impianti industriali. Quindi, dagli anni settanta, quando i PLC sono stati introdotti per la prima volta sul mercato, hanno dominato i processi e il mercato dell’automazione industriale. Tuttavia, dai primi anni novanta a oggi, il PC industriale si è fatto molto avanti in questi mercati, grazie alla gamma e alla velocità dei processori che continua ad aumentare e allo stesso tempo il costo di questi componenti continua a diminuire. Il numero di applicazioni che utilizzano PC è in crescita, provocando uno sviluppo accelerato che confonde il confine tra le due tecnologie. Dieci anni fa scegliere quale soluzione di automazione da usare sarebbe stato facile, oggi non è più così. Il PLC è stato inventato per essere dedicato a specifici compiti in fabbrica dove era necessario garantire un’ottima robustezza e assicurare prestazioni costanti in ambienti difficili alla presenza di livelli relativamente alti di interferenze e vibrazioni. Col passare del tempo, il PLC si è evoluto per includere la capacità di gestire il motion control, i processi di controllo avanzato Pid e di sicurezza integrata, adottando anche alcune caratteristiche dei PC, come ad esempio il web server e le utility di rete. Il PC in origine aveva un ruolo diverso ed era utilizzato principalmente per calcoli complessi, monitoraggio, misura e nel networking di fabbrica, ma anche come interfaccia utente per il PLC. Era in genere installato in un locale più controllato dal punto di vista ambientale, poiché non poteva lavorare in modo tanto efficace quanto un PLC nelle più difficili condizioni produttive. Il PC si è poi evoluto al punto di comprendere le funzionalità del PLC, pur mantenendo le sue capacità chiave. Il PC è diventato anche un controller più robusto, adatto a lavorare in ambienti difficili come era possibile una volta soltanto per i PLC. Nell’analizzare l’architettura di controllo possiamo segnalare una certa convergenza delle tecnologie. Con l’aggiunta di una card Pci, di driver hardware e software si può trasformare il PC in quello che è conosciuto genericamente come un soft-plc.Inoltre, si può implementare un kernel real-time per supportare i compiti tecnicamente più critici. Il PAC si è sviluppato proprio a seguito di queste importanti integrazioni funzionali.
Indicazioni generali per scegliere la soluzione tecnica
Si possono fornire indicazioni di come scegliere tra un tipo di controllo di automazione o un altro? Per scegliere un PCo un PLC o un sistema ibrido, è importante definire inizialmente come semplificare la decisione analizzando e comparando alcune delle caratteristiche che potrebbero differenziare le tecnologie. Potremmo così identificare alcuni elementi principali da tenere in considerazione per quest’analisi comparativa. Necessiterà analizzare come “lavora” il sistema operativo e come vengono processate le istruzioni e i task, un aspetto che diventa più complesso nel caso si vada verso controlli real time e ne discende l’affidabilità del componente. Un altro aspetto da tenere in considerazione è la robustezza specialmente in ambienti industriali critici. Si devono poi considerare la reperibilità dei componenti di ricambio,e la semplicità/tempi di riparazione. Bisogna valutare i requisiti per la comunicazione, l’interfaccia per il bus di campo, la memoria, la potenza del processore e l’integrazione con l’Hmi. Vi sono poi elementi legati alla security e alla safety (per esempio funzioni integrate).La definizione dell’hardware si porta spesso dietro la scelta dell’ambiente e del linguaggio usati per la programmazione, scelta che influisce sull’operatività e sui tempi di sviluppo dell’applicazione. Anche il prezzo della soluzione è importante poiché a seconda delle applicazioni l’impiego di una tecnologia diversa può comportare notevoli differenze economiche che dipendono essenzialmente dalle performance desiderate, dal livello di espandibilità che si vuole ottenere e dall’ambiente in cui opera la soluzione scelta.
a cura di Carlo Marchisio
………………………………………………………………………………………………………….
Il parere dell’esperto
Tendenze nei dispositivi di controllo per l’automazione industriale
I dispositivi di controllo più utilizzati nell’automazione industriale sono: PC industriali, PLC e PAC. I PC industriali sono piattaforme, basate su microprocessore e dotate di software custom oppure standard, che vengono utilizzate per applicazioni quali il controllo di processi o l’acquisizione di dati. Un PLC (Programmable Logic Controller) è un dispositivo digitale dedicato al controllo di sistemi meccatronici, caratterizzato dalla possibilità di programmare, in maniera relativamente semplice, gli output del sistema in funzione degli input. Esso può essere programmato sia in linguaggio evoluto (C, C++ o addirittura nel linguaggio dedicato “State Logic”), sia in logica elementare “a relé”. Quest’ultima modalità di programmazione costituisce un retaggio dell’origine del PLC, che inizialmente era basato sulla programmazione di singole porte logiche. Con l’acronimo PAC (Programmable Automation Controller) si designa invece un dispositivo, di origine più recente rispetto ai PC industriali e ai PLC, che combina le caratteristiche e le prestazioni di un sistema di controllo basato su microprocessore con quelle di un PLC. A differenza dei PC industriali e dei PLC, i PAC sono nati quando Internet era già una realtà, e quindi sono caratterizzati dal fatto di possedere, già integrate, delle funzionalità di networking su protocolli quali TCP/IP, SMTP ecc. I PAC vengono utilizzati per le medesime applicazioni dei PLC; tuttavia essi presentano architetture più aperte e modulari, e non hanno. in generale, la possibilità di essere programmati nella “vecchia”logica sequenziale tipica dei PLC. Quali sono le principali tendenze nel settore dei dispositivi di controllo? Se ne possono individuare sostanzialmente tre:
- Connettività – I tre classici livelli di un sistema automatico (il livello “office”, il livello “controller” e il livello “field”) vedono aumentare la necessità di comunicare e di scambiarsi informazioni. I dispositivi di controllo, pertanto. accentuano le proprie caratteristiche di connettività, di flessibilità e programmabilità. I PC industriali, i PLC e i PAC devono essere in grado di gestire la notevole varietà di protocolli di comunicazione esistenti, per mezzo di hardware e firmware programmabili che permettano ai progettisti di sistema di supportare una molteplicità di protocolli utilizzando lo stesso processore. Inoltre, la grande varietà di sensori a cui i dispositivi si devono interfacciare determina una forte spinta alla connettività.
- Integrazione – Gli sviluppi dell’automazione industriale hanno portato all’aumento del numero di canali, e ad una tendenza alla loro collocazione remota. Ai dispositivi di controllo è pertanto richiesto un aumento della capacità di calcolo, oltre ad una riduzione delle dimensioni. Ciò può essere ottenuto mediante il ricorso ad una maggiore integrazione delle funzioni e dei canali presenti nei dispositivi stessi, ad esempio con l’utilizzo di sistemi embedded, i quali presentano spiccate caratteristiche di integrazione e di ubiquità.
- Sicurezza funzionale – Negli ultimi anni la complessità dei sistemi automatici è aumentata notevolmente: ciò comporta, in caso di malfunzionamento, una maggiore probabilità di danni ai macchinari e alle persone. Allo stesso tempo, sono entrate in vigore normative sempre più stringenti relative ai livelli e agli standard di sicurezza. I dispositivi di controllo devono quindi garantire un livello ben più elevato di sicurezza funzionale, in generale raggiunta mediante caratteristiche aggiuntive di diagnostica integrata (ad esempio self-test automatici) e di ridondanza funzionale, in modo tale da ridurre drasticamente la probabilità di guasto del sistema. Queste caratteristiche aggiuntive di sicurezza cominciano ad essere integrate negli stessi dispositivi di controllo, anziché essere delegate a dispositivi dedicati, quali ad esempio i safety PLC. Nel settore automotive già da qualche tempo vengono usati processori dual core che operano in sincronia: si prevede che questa pratica si estenderà presto al settore industriale in genere.
Alessandro Gasparetto
Professore Ordinario di Meccanica Applicata alle Macchine Docente del corso di “Meccatronica e Robotica”, Dipartimento di Ingegneria Elettrica, Gestionale e Meccanica Università di Udine
…………………………………………………………………………………………………………..
…………………………………………………………………………………………………………..
LA PAROLA A…
Alberto Griffini
Channel Manager di GE Intelligent Platforms, Filiale Italiana

GE Intelligent Platforms è la divisione di GE che fornisce le più recenti tecnologie ad elevate prestazioni nell’ambito dell’Automazione Industriale con una vasta gamma di prodotti che vanno dal controllore al sistema di supervisione, offrendo software, hardware, servizi, competenze ed esperienza.
Il ruolo nell’automazione dei tre prodotti. Aree diverse, integrazioni… Le sue considerazioni.
Il PAC ha rappresentato l’evoluzione del PLC verso tecnologia e design tipici del PC. Con il PAC l’hardware e le funzionalità del PLC si sono molto avvicinate al PC industriale. La nostra nuova piattaforma PACSystems RXi utilizza la stessa scheda CPU COMExpress per entrambe le versioni: PC e Controllore, offrendo una soluzione modulare e versatile per applicazioni OEM, RTU e controllo d’impianto produttivo.
Le reti di comunicazioni per questi componenti sono comuni oppure vi sonopunti da evidenziare?
L’aspetto comunicazioni standard in comune è sempre più spinto: ethernet, industrial internet, wi-fi, USB sono chiari esempi di come la tecnologia PC sia ormai diffusa nell’ambito del Controllo Industriale basato su PLC o PAC. La caratteristica di base è ovviamente la robustezza dell’hardware, superiore a quella disponibile nel mercato del Consumer.
Sue considerazioni sul back-up di questi sistemi. Sono richiesti accorgimenti particolari?
A seconda delle richieste di disponibilità del sistema di controllo, quindi di elevati valori di MTBF (Mean Time Between Failure) si possono prevedere soluzioni ridondanti di CPU, comunicazione e ingressi/uscite. Le architetture denominate hot-backup prevedono l’intervento dell’unità secondaria in tempo reale in caso di guasto della primaria, senza creare interruzioni di controllo del sistema e di produzione.
Integrazioni dei sistemi SCADA: particolari considerazioni utilizzando i sistemi indicati.
La classica separazione tra SCADA e Controllore si può dire superata grazie alle nuove soluzioni che utilizzano Soft PLC basati su PC oppure piattaforme integrate di tipo modulare. Questo consente da un lato di ridurre i costi dell’hardware e dall’altro di aumentare le prestazioni in termini di velocità di elaborazione e di raccolta dati. L’utilizzo di CPU multi-core indica la strada verso cui prevedibilmente evolveranno i sistemi di controllo per integrarsi in un unico prodotto.
Controllore PACSystems® RXi. Presenta connettività Gigabit Ethernet ed oltre al design compatto e accattivante e alla possibilità di combinarlo con il modulo IPC della serie, offre un’interfaccia ridondata PROFINET integrata. Con 2 GB di Ram, processore Dual Core su scheda COMExpress, offre elevata connettività
grazie a 2 porte GB PROFINET ed una GB Ethernet, oltre a 2 USB tradizionali ed una micro USB. Può essere combinato con il modulo display touch screen intelligente: grazie a questo è possibile effettuare tutte le operazioni di manutenzione e di controllo, direttamente a bordo macchina. Da un punto di vista della gestione verso il campo, il controllore RXi rappresenta una svolta rispetto ai sistemi tradizionali: non presenta I/O locali permettendo in tal modo l’espansione in modo totalmente flessibile.
………………………………………………………………………………………………………..
Nicoletta Ghironi
Responsabile Marketing e Comunicazione di B&R Automazione Industriale.
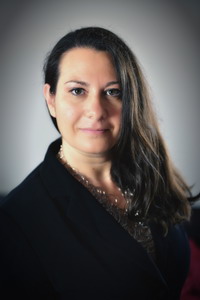
B&R è uno dei riferimenti tecnologici più importanti nella fornitura di sistemi di automazione per costruttori di macchine e sistemi con una proposta completa di soluzioni innovative: controllo, motion, visualizzazione, safety e comunicazione, tutte armonizzate attraverso Automation Studio.
Perchè il design industriale per PC industriali, PLC e PAC è un argomento importante per gli utilizzatori?
Sono tanti gli aspetti su cui l’ingegnerizzazione di un prodotto ha effetto.Un design meccanico ed elettrico a regola d’arte possono fare la differenza in termini di prestazioni operative: robustezza, durata, disponibilità, accessibilità e manutenibilità nel tempo, e di sicurezza e di testabilità del prodotto – una qualità “nascosta” all’utilizzatore, ma che ha effetti sulla diagnostica e sulla garanzia di funzionamento. La combinazione di un buon design con buone tecnologie costruttive permette di soddisfare anche esigenze particolari: l’impiego in ambienti estremi richiede dispositivi con livelli di protezione elevati e range estesi di funzionamento.L’uso in luoghi regolamentati, dove l’igiene dev’essere garantita o ancora dove non si devono accumulare polveri, richiede soluzioni ad hoc, come i pannelli in acciaio inox.con livello di protezione elevato e con superficie frontale perfettamente liscia e igienizzabile.Un ultimo aspetto del design riguarda l’ergonomia, ormai importante anche nell’industria.E di pari passo con l’ergonomia cresce la domanda di personalizzazione dei prodotti, perché aderiscano il più possibile alle specifiche esigenze applicative e costituiscano un tratto distintivo e d’immagine sul proprio mercato.
Il software di sviluppo: una sua analisi sugli sviluppi tecnici.
L’obiettivo è chiaro: ottimizzare lo sviluppo delle applicazioni in modo da ridurre il più possibile gli sforzi e i tempi di realizzazione.Il software del futuro deve venire in aiuto semplificando la vita del progettista e noicon Automation Studio supportiamo queste esigenze.Ad esempio permettendo di usare un unico software per programmare la logica di controllo, il controllo di parti in movimento (motori, robot, CNC), la visualizzazione / interfaccia grafica, oltre che per tutti gli aspetti di progettazione, simulazione, debugging, test e gestione del progetto. In questo modo è sufficiente prendere dimestichezza con un solo strumento di sviluppo e non ci sono problemi di interazione o di compatibilità tra una parte e l’altra.Oltre a comprendere tutti questi aspetti, l’ideale sarà poter portare un’applicazione sviluppata per PLC su un pannello intelligente o su un computer industriale, senza cambiare una sola linea di codice, rendendo possibile un cambio di piattaforma hardware, scalare il sistema in un secondo momento, creare differenti versioni del sistema, senza mai ritoccare il programma.Altra caratteristica indispensabile è la capacità di integrare parti di programma già esistenti, senza doverli riscrivere, riutilizzandoli per progetti futuri, adottando standard industriali per i linguaggi di programmazione, per le comunicazioni e per lo scambio di dati e metadati.L’ultima tendenza è poi quella di offrire al programmatore degli strumenti che lo aiutino a configurare e a creare, in modo grafico e intuitivo, un’applicazione dal nulla. Per tutte le applicazioni più comuni lo strumento di sviluppo semplificherà molto e permetterà, in pochissimo tempo, di avere un’applicazione funzionante.
I costruttori di macchine come vedono i diversi dispositivi di controllo? Alcune loro considerazioni.
Ogni piattaforma è nata per far fronte a esigenze e impieghi differenti ma, con il passare degli anni e lo sviluppo di tecnologie di elaborazione sempre più potenti, robuste e affidabili, le differenze si assottigliano e, pur non evidenziandolo in modo esplicito, molti dispositivi che ancora oggi chiamiamo PLC, sono oggi realizzati con tecnologie embedded che – tolto il fattore di forma fisico (PLC/PAC modulare, pannello, PC industriale) – li rendono, di fatto, tutti dei computer industriali che implementano il controllo in una forma che si è usi definire softPLC.
Dal punto di vista funzionale, di programmabilità e di interfacce, gli stessi dispositivi embedded possono ricadere tranquillamente nella categoria PAC, anche se dal punto di vista del marketing non si sceglie di battezzarli con tale acronimo.Chiarito quindi che, salvo eccezioni che ancora utilizzano tecnologie tradizionali, le moderne piattaforme di controllo sono potenzialmente equiparabili e consentono di realizzare più cicli di controllo paralleli in tempo reale, possono essere programmati in ambienti grafici e con linguaggi IEC standard, sono dotate di interfacce evolute verso i bus di campo standard e possono avere interfacce uomo-macchina evolute, grafiche e remotabili. Le uniche valutazioni che possono aiutare nella scelta, a seconda dell’impiego, sono il formato (peso, dimensioni, attacco), potenza, livello di protezione, livello di integrazione e dotazione di interfacce.
Come vede l’integrazione di questi prodotti a bordo macchina?
Distinguiamo tra interazione delle diverse parti dell’automazione e inserimento dei dispositivi nella struttura fisica della macchina.Il primo punto, l’integrazione logica delle diverse parti del sistema di automazione, è uno degli obiettivi principe di ogni costruttore di automazione.Noi abbiamo riconosciuto l’importanza di una completa e nativa integrazione tra ogni singola parte del controllo, della visualizzazione, della raccolta dati e – oggi più che mai – delle funzioni di sicurezza. Questa capacità di colloquiare di tutte le parti in gioco agevola il programmatore nel suo lavoro. Ogni scambio di dati avviene attraverso i bus di comunicazione, e dato che spesso costituiscono un collo di bottiglia, anche questi assumono un ruolo determinante. Noi, pur offrendo anche la comunicazione con altri bus industriali, abbiamo scelto di adottare Powerlink, un bus di comunicazione real-time ad alte prestazioni, basato su standard Ethernet e tecnologia open-source, per garantire nel tempo la massima apertura e flessibilità. La topologia di connessione e i relativi cablaggi tra i dispositivi hanno un effetto anche sulla parte fisica della macchina: un cablaggio semplice la rende più pulita, ordinata, semplice e veloce da cablare e manutenere, oltre che meno costosa.
Robusto e affidabile, con disponibilità a lungo termine: sono queste le caratteristiche che contraddistinguono l’Automation PC910, il nuovo PC compatto offerto da B&R. La nuova tecnologia Intel® Core™ i di terza
generazione è il cuore di questo potente PC industriale. Le CPU Core™ i3, Core™ i5 e Core™ i7 con fino a quattro core combinati con il recentissimo chipset QM77 Express forniscono il più elevato livello di prestazioni attualmente disponibili su computer industriali.
……………………………………………………………………………………………………
Roberto Motta
Local Business Leader IA-Italian Region Rockwell Automation
Rockwell Automation, è leader mondiale nella fornitura soluzioni per l’automazione, per il controllo e per l’IT che aiutano i produttori a ottenere vantaggio competitivo nel proprio business in modo sostenibile: la società impiega circa 21.000 dipendenti e serve clienti in più di 80 paesi.
Scelta tecnica di PC industriali, PLC e PAC. Considerazioni in base alla tipologia di Applicazione (processo, macchinario)
Generalmente viene preso in considerazione l’uso di un PAC rispetto a un PLC se l’applicazione richiede:algoritmi di controllo avanzati, modifica estesa dei database, routine di controllo personalizzate integrate, simulazione di processi complessi e necessità di taglie di memoria elevate.Genericamente poi i controllori di automazione programmabili (PAC) sono controlloridi tipo multidisciplinare (processo, discreto, batch, safety e Motion/drive in un unico controllore) e scalabili facilmente integrabili in un’architettura aperta e modulare. I controllori PAC di ultima generazione quali i nostri Logix hanno un sistema operativo multitasking, una struttura della memoria basata su tag, supportano lo stesso set di istruzioni e hanno una struttura logica e linguaggi di programmazione conformi allo standard (IEC 61131-3) attuale.
I vostri clienti sono attenti sulle scelte applicative.Richiedono la vostra consulenza?
Per le applicazioni più complesse è possibile che sia richiesta la nostra consulenza. Le nostre soluzioni di controllo sono altamente integrate e aiutano a risolvere facilmente le sfide legate alla moderna produzione: riduzione dei costi, aumento della produttività, miglioramento della qualità e incremento della flessibilità. I nostri prodotti sono progettati per funzionare insieme, e consentono di ottenere notevoli vantaggi in termini di risparmio di tempo, riduzione dei costi e avvio più rapido.
Considerazioni per gli input/output da utilizzare: a bordo macchina oppure nelquadro elettrico?
Nella scelta rientrano le esigenze di ogni applicazione, i tempi di risposta richiesti, il numero di nodi I/O e loro distanza. Da tempo molte applicazioni quali quelle di controllo di macchine automatiche hanno operato scelte verso un utilizzo largamente diffuso di I/O a bordo macchina. Anche nel caso di I/O in quadro elettrico l’opzione preferenziale è sempre di più quella di I/O studiati per essere applicati originariamente a bordo macchina.Stiamo parlando, nella stragrande maggioranza dei casi, di I/O che vanno ubicati comunque in piccoli quadri di derivazione anche a bordo macchina piuttosto che direttamente con grado di protezione IP67. La larga diffusione di I/O remotati a bordo macchina in armadio è strettamente legata ai tempi di risposta garantiti dalle moderne tecniche di fieldbus, quale p.e. EtherNet/IP in grado di ottimizzare molto più che in passato l’utilizzo della banda di trasmissione della rete.Il numero di nodi I/O e la lunghezza della rete sono gli altri elementi chiave della scelta; con l’aumentare del numero dei nodi, un cablaggio a bordo macchina diviene economicamente vincente, come anche all’aumentare delle distanze il risparmio nella stesura dei cavi I/O diviene più significativo.
Considerazioni sulla diagnostica ed allarmi legata alla scelta del sistema utilizzato. Indicazioni e consigli.
Le informazioni relative ad una diagnostica puntuale stanno divenendo sempre più importanti per ridurre i tempi di fermo macchina o per evitarli del tutto. Una caratteristica molto innovativa resa facilmente disponibile dall’utilizzo della tecnologia TCP/IP anche a livello Fieldbus (p.e. EtherNet/IP) è rappresentata dalla possibilità di gestire informazioni diagnostiche relative anche a semplici nodi I/O utilizzando un generico Internet Browser. P.e. ogni nodo di Rockwell Automation per EtherNet/IP dispone di un’interfaccia web, e da qualsiasi computer, digitando l’indirizzo IP del modulo come URL, i dati relativi al nodo sono visualizzati direttamente su pagine HTML.
I Controllori di automazione programmabili della famiglia Logix sono controllori di tipo multidisciplinare (processo, discreto, batch, safety e Motion/drive in un unico controllore) e scalabili
facilmente integrabili in un’architettura aperta e modulare.
………………………………………………………………………………………………………..
Antonio Marra, Operational Marketing Executive per l’offerta Advanced Motion in Schneider Electric
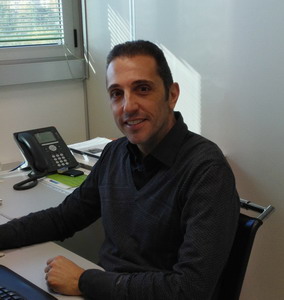
Schneider Electric è lo specialista globale nella gestione dell’energia, offre soluzioni integrate in diversi segmenti di mercato, con una posizione di leadership nei settori energia e infrastrutture, processi industriali, building automation e data center, vantando inoltre un’ampia presenza nelle applicazioni residenziali.
Il mercato dell’automazione ha bisogno di maggior sicurezza informatica. Una sua opinione su argomento.
Lo sviluppo delle reti di comunicazione –tipicamente su base Ethernet- unito alla sempre maggiore integrazione delle tecnologie informatiche a tutti i livelli del processo produttivo, obbliga oggi i fornitori e gli utilizzatori di automazione, a porre una sempre maggiore attenzione al Data Security. Infatti, oggi, per un manutentore di linea è normale collegarsi attraverso un cavo Ethernet a un PC e a un Controller di macchina. Quest’ultimo, essendo sicuramente collegato ad un pannello operatore, apre subito la prima falla verso l’acceso a dati sensibili come le ricette di produzione. Da questo punto in avanti il gioco è semplice. Controller collegati tra loro sulla linea di produzione e linee collegate a strumenti di gestione aziendale aprono la via per l’acceso a dati tipicamente oggi considerati esclusiva del mondo “office”.
? Controllo di processo: verifichiamo un maggior utilizzo di PLC, PC e PAC. Ci saranno nuovi sviluppi?
Sicuramente già oggi il PLC è un attore importante. Per quanto riguarda il PAC o il suo più prossimo parente, il PC, i margini di applicabilità nel futuro saranno sicuramente sempre maggiori. Probabilmente oggi ancora non sono pronti al 100% per sostituire il PLC – in particolar modo nelle applicazioni più tipiche del controllo di processo- ma ritengo che entrambe le soluzioni mettano a disposizione una capacità di calcolo e di configurabilità che sicuramente le farà diventare i principali attori in futuro ormai non lontanissimo.
Gli End User intervengono sulle scelte tecniche di queste soluzioni, oppure delegano gli OEM?
Sicuramente, per quanto riguarda il mondo macchine i grossi End-User influiscono fortemente sulla scelta di alcune tecnologie. Principalmente le prescrizioni sono presenti su tecnologie come PLC, pannelli operatore (HMI), periferiche di campo (I/O). In generale, anche se la tendenza incomincia a cambiare, non esistono ancora pressioni per la scelta dei sistemi come ad esempio il Motion Control. Questi sono ancora “culturalmente” distanti dalle conoscenze degli utilizzatori finali. Ovviamente poi intervengono fattori come la disponibilità dei ricambi, la storicità dei plant (stesso End-User su plant diversi può avere prescrizioni diverse), il livello di conoscenza di determinati sistemi.
Sviluppi futuri dell’automazione degli impianti. Unico hardware potente, centralizzato oppure più sistemi decentrati collegati in rete?
Direi che la tendenza è quella di decentralizzare gli attuatori ma centralizzare l’intelligenza. Ovviamente esistono diversi “livelli” di intelligenza. Se guardiamo ad esempio una linea di produzione, vediamo come questa stia lentamente compattandosi, diventando, dal punto di vista dell’intelligenza, una macchina. La potenza di calcolo dei controllori permette di integrare in un unico dispositivo funzionalità che prima erano distribuite su più unità (es. il numero di servoassi controllati). In questo modo si risparmia in termini di numero di unità di controllo, si eliminano le interfacce di scambio dati, si semplifica il debugging dei SW, si riescono a velocizzare operazioni sincronizzate. Sul lato attuatori invece, la tendenza è esattamente quella contraria. I motivi sono diversi: risparmio nel cablaggio, flessibilità nel realizzare la configurazione, minor spazio occupato dai quadri elettrici. Ovviamente per aumentare questo livello di decentralizzazione il ruolo delle reti di comunicazione diventa fondamentale. Ecco che sistemi basati sulla tecnologia Ethernet, anche se con protocolli diversi, conquistano sempre maggiori spazi.
I controller LMC 101C e 201C completano la serie LMC. Coprono una vasta gamma di applicazioni ed sono in grado di offrire la miglior soluzione con un giusto rapporto fra prezzo e performance, in funzione del numero di assi da sincronizzare, del volume di dati da trasmettere e degli elementi di ro
botica da integrare. I modelli LMC 101C e LMC 201C sono pensati per sincronizzare rispettivamente fino a 4 e 8 assi; prevedono CANopen come bus di campo e connessione Ethernet integrata che funge sia da interfaccia con il programma di sviluppo, con gli elementi HMI mediante OPC, ARTI o Modbus TCP, sia da interfaccia aperta per realizzare soluzioni di comunicazione personalizzate.
Analisi: PC industriali, PLC e PAC
Un controllore di automazione programmabile (PAC) è un controller compatto, che unisce le caratteristiche e le funzionalità di un PC basato su sistema di controllo con quella di un tipico controllore logico programmabile (PLC).I sistemi PAC sono più spesso utilizzati in ambienti industriali per il controllo di processo, acquisizione dati, apparecchiature di monitoraggio a distanza, visione artificiale e controllo del movimento. Inoltre, perché funzionano e comunicano con interfaccia di rete tramite protocolli quali TCP / IP, OLE for Process Control (OPC) e SMTP,i PAC sono in grado di trasferire i dati dalle macchine che controllano ad altre macchine. L’ARC Advisory Group, un gruppo analista focalizzato sul settore manifatturiero, è generalmente accreditato per avere creato il termine “PAC”. È stato coniato nel 2001 come un modo per aiutare gli utenti di hardware di controllo a definire meglio le loro esigenze, e di dare ai principali fornitori di hardware di controllo un termine per comunicare più chiaramente le potenzialità dei loro prodotti. In generale, PAC e PLC servono allo stesso scopo. Entrambi sono utilizzati principalmente per eseguire l’automazione, controllo di processo, e le funzioni di acquisizione dati, digitali e analogici di controllo, gestione delle stringhe di serie, PID, controllo del movimento, e la visione della macchina. I parametri entro i quali operano PAC per raggiungere questo obiettivo, tuttavia, sono a volte in contrasto con il funzionamento delle funzioni PLC. A differenza dei PLC, che costantemente attuano la scansione di tutti gli I/O nel sistema di controllo a velocità molto elevate, PAC utilizza un unico database tagname e un indirizzo logico di sistema per identificare e mappare i punti di I/O in base alle esigenze. I computer industriali invece rivestono un ruolo di primaria importanza sia a livello di area (workstation, potenti elaboratori…) sia a livello di cella (PC industriali o computer modulari per la realizzazione di sistemi di supervisione, controllo di processo, interfaccia operatore…). Sono dotati di elevato potere di calcolo, si interfacciano facilmente ad altri computer, con i quali possono condividere dati e programmi, consentono la gestione diretta di segnali anche non numerici, sono dotati di software di base che semplifica la programmazione e la gestione da parte dell’utente. Il computer si è evoluto dall’ambiente dell’ufficio all’area industriale grazie alla sua versatilità, semplicità d’uso e diffusione ed è stato adattato a questo nuovo ambito di lavoro rendendo più affidabile il software e più robusto l’hardware.
Elemento tecnologico importante: il software
Con il termine PAC (Programmable Automation Controller), si evidenziano dei controller compatti o modulari ibridi che combinano le caratteristiche e le capacità di un sistema di controllo basato su processore PC con quella di un tipico controller logico programmabile. I PLC (Programmable Logic Controller) sono strutturati come dei microcomputer industriali e sono utilizzati principalmente per eseguire l’automazione, il controllo dei processi e le funzioni di acquisizione dei dati, come il controllo real-time dei segnali digitali e analogici, la gestione di calcoli complessi su variabili e array, il controllo del movimento, la gestione dei Pid, la diagnostica, il controllo a distanza. Considerando la grande differenza tra i piccoli e i grandi PLC, i programmi possono essere molto semplici ma anche molto articolati e complessi. Spesso sono ampiamente supportati da software di base che permettono l’utilizzo di linguaggi con macrofunzioni, simbolici o simil-grafici. La differenza di base tra un PAC e un PLC è da analizzare per la componente software, che permette di avere a disposizione un linguaggio di programmazione grafico intuitivo, simile a uno schema di flusso, ma associato a sistemi operativi real-time e con possibilità di definizione di hardware riconfigurabile. I programmi di controllo sono in genere sviluppati con strumenti software generici che permettono di progettare il programma per essere condiviso tra più computer, processori, terminali Hmi o altri componenti dell’architettura del sistema di controllo. I PAC sono particolarmente adatti alle comunicazioni che sfruttano protocolli standard e interfacce di rete e sono solitamente racchiusi in contenitori non più grandi di quello di un comune PLC: in tale spazio trovano posto un microprocessore evoluto, svariati moduli di memoria (sia volatile che permanente), moduli di controllo assi e diversi modelli d’interfaccia di comunicazione. L’intelligenza di bordo è fornita dai tools di un sistema operativo, tipicamente in tempo reale in grado di offrire bassi tempi di latenza e un determinismo adatto all’impiego in compiti critici, e da un software applicativo evoluto che è solitamente realizzato su piattaforme di sviluppo di tipo PC e successivamente “scaricato” nel dispositivo. Nel panorama odierno tutti i principali fornitori di automazione propongono entrambe le soluzioni, e la tendenza generale è comunque quella di chiamare PLC un sistema che ha le caratteristiche prestazionali di PAC.
Alcune tappe dell’evoluzione tecnologica
I PLC hanno sempre contribuito ai progressi nel campo del controllo delle macchine automatiche, dai piccoli controlli usati nelle macchine operative, ai controlli su ampia scala destinati al comando di complessi impianti industriali. Quindi, dagli anni settanta, quando i PLC sono stati introdotti per la prima volta sul mercato, hanno dominato i processi e il mercato dell’automazione industriale. Tuttavia, dai primi anni novanta a oggi, il PC industriale si è fatto molto avanti in questi mercati, grazie alla gamma e alla velocità dei processori che continua ad aumentare e allo stesso tempo il costo di questi componenti continua a diminuire. Il numero di applicazioni che utilizzano PC è in crescita, provocando uno sviluppo accelerato che confonde il confine tra le due tecnologie. Dieci anni fa scegliere quale soluzione di automazione da usare sarebbe stato facile, oggi non è più così. Il PLC è stato inventato per essere dedicato a specifici compiti in fabbrica dove era necessario garantire un’ottima robustezza e assicurare prestazioni costanti in ambienti difficili alla presenza di livelli relativamente alti di interferenze e vibrazioni. Col passare del tempo, il PLC si è evoluto per includere la capacità di gestire il motion control, i processi di controllo avanzato Pid e di sicurezza integrata, adottando anche alcune caratteristiche dei PC, come ad esempio il web server e le utility di rete. Il PC in origine aveva un ruolo diverso ed era utilizzato principalmente per calcoli complessi, monitoraggio, misura e nel networking di fabbrica, ma anche come interfaccia utente per il PLC. Era in genere installato in un locale più controllato dal punto di vista ambientale, poiché non poteva lavorare in modo tanto efficace quanto un PLC nelle più difficili condizioni produttive. Il PC si è poi evoluto al punto di comprendere le funzionalità del PLC, pur mantenendo le sue capacità chiave. Il PC è diventato anche un controller più robusto, adatto a lavorare in ambienti difficili come era possibile una volta soltanto per i PLC. Nell’analizzare l’architettura di controllo possiamo segnalare una certa convergenza delle tecnologie. Con l’aggiunta di una card Pci, di driver hardware e software si può trasformare il PC in quello che è conosciuto genericamente come un soft-plc.Inoltre, si può implementare un kernel real-time per supportare i compiti tecnicamente più critici. Il PAC si è sviluppato proprio a seguito di queste importanti integrazioni funzionali.
Indicazioni generali per scegliere la soluzione tecnica
Si possono fornire indicazioni di come scegliere tra un tipo di controllo di automazione o un altro? Per scegliere un PCo un PLC o un sistema ibrido, è importante definire inizialmente come semplificare la decisione analizzando e comparando alcune delle caratteristiche che potrebbero differenziare le tecnologie. Potremmo così identificare alcuni elementi principali da tenere in considerazione per quest’analisi comparativa. Necessiterà analizzare come “lavora” il sistema operativo e come vengono processate le istruzioni e i task, un aspetto che diventa più complesso nel caso si vada verso controlli real time e ne discende l’affidabilità del componente. Un altro aspetto da tenere in considerazione è la robustezza specialmente in ambienti industriali critici. Si devono poi considerare la reperibilità dei componenti di ricambio,e la semplicità/tempi di riparazione. Bisogna valutare i requisiti per la comunicazione, l’interfaccia per il bus di campo, la memoria, la potenza del processore e l’integrazione con l’Hmi. Vi sono poi elementi legati alla security e alla safety (per esempio funzioni integrate).La definizione dell’hardware si porta spesso dietro la scelta dell’ambiente e del linguaggio usati per la programmazione, scelta che influisce sull’operatività e sui tempi di sviluppo dell’applicazione. Anche il prezzo della soluzione è importante poiché a seconda delle applicazioni l’impiego di una tecnologia diversa può comportare notevoli differenze economiche che dipendono essenzialmente dalle performance desiderate, dal livello di espandibilità che si vuole ottenere e dall’ambiente in cui opera la soluzione scelta.
a cura di Carlo Marchisio
………………………………………………………………………………………………………….
Il parere dell’esperto
Tendenze nei dispositivi di controllo per l’automazione industriale
I dispositivi di controllo più utilizzati nell’automazione industriale sono: PC industriali, PLC e PAC. I PC industriali sono piattaforme, basate su microprocessore e dotate di software custom oppure standard, che vengono utilizzate per applicazioni quali il controllo di processi o l’acquisizione di dati. Un PLC (Programmable Logic Controller) è un dispositivo digitale dedicato al controllo di sistemi meccatronici, caratterizzato dalla possibilità di programmare, in maniera relativamente semplice, gli output del sistema in funzione degli input. Esso può essere programmato sia in linguaggio evoluto (C, C++ o addirittura nel linguaggio dedicato “State Logic”), sia in logica elementare “a relé”. Quest’ultima modalità di programmazione costituisce un retaggio dell’origine del PLC, che inizialmente era basato sulla programmazione di singole porte logiche. Con l’acronimo PAC (Programmable Automation Controller) si designa invece un dispositivo, di origine più recente rispetto ai PC industriali e ai PLC, che combina le caratteristiche e le prestazioni di un sistema di controllo basato su microprocessore con quelle di un PLC. A differenza dei PC industriali e dei PLC, i PAC sono nati quando Internet era già una realtà, e quindi sono caratterizzati dal fatto di possedere, già integrate, delle funzionalità di networking su protocolli quali TCP/IP, SMTP ecc. I PAC vengono utilizzati per le medesime applicazioni dei PLC; tuttavia essi presentano architetture più aperte e modulari, e non hanno. in generale, la possibilità di essere programmati nella “vecchia”logica sequenziale tipica dei PLC. Quali sono le principali tendenze nel settore dei dispositivi di controllo? Se ne possono individuare sostanzialmente tre:
- Connettività – I tre classici livelli di un sistema automatico (il livello “office”, il livello “controller” e il livello “field”) vedono aumentare la necessità di comunicare e di scambiarsi informazioni. I dispositivi di controllo, pertanto. accentuano le proprie caratteristiche di connettività, di flessibilità e programmabilità. I PC industriali, i PLC e i PAC devono essere in grado di gestire la notevole varietà di protocolli di comunicazione esistenti, per mezzo di hardware e firmware programmabili che permettano ai progettisti di sistema di supportare una molteplicità di protocolli utilizzando lo stesso processore. Inoltre, la grande varietà di sensori a cui i dispositivi si devono interfacciare determina una forte spinta alla connettività.
- Integrazione – Gli sviluppi dell’automazione industriale hanno portato all’aumento del numero di canali, e ad una tendenza alla loro collocazione remota. Ai dispositivi di controllo è pertanto richiesto un aumento della capacità di calcolo, oltre ad una riduzione delle dimensioni. Ciò può essere ottenuto mediante il ricorso ad una maggiore integrazione delle funzioni e dei canali presenti nei dispositivi stessi, ad esempio con l’utilizzo di sistemi embedded, i quali presentano spiccate caratteristiche di integrazione e di ubiquità.
- Sicurezza funzionale – Negli ultimi anni la complessità dei sistemi automatici è aumentata notevolmente: ciò comporta, in caso di malfunzionamento, una maggiore probabilità di danni ai macchinari e alle persone. Allo stesso tempo, sono entrate in vigore normative sempre più stringenti relative ai livelli e agli standard di sicurezza. I dispositivi di controllo devono quindi garantire un livello ben più elevato di sicurezza funzionale, in generale raggiunta mediante caratteristiche aggiuntive di diagnostica integrata (ad esempio self-test automatici) e di ridondanza funzionale, in modo tale da ridurre drasticamente la probabilità di guasto del sistema. Queste caratteristiche aggiuntive di sicurezza cominciano ad essere integrate negli stessi dispositivi di controllo, anziché essere delegate a dispositivi dedicati, quali ad esempio i safety PLC. Nel settore automotive già da qualche tempo vengono usati processori dual core che operano in sincronia: si prevede che questa pratica si estenderà presto al settore industriale in genere.
Alessandro Gasparetto
Professore Ordinario di Meccanica Applicata alle Macchine Docente del corso di “Meccatronica e Robotica”, Dipartimento di Ingegneria Elettrica, Gestionale e Meccanica Università di Udine
…………………………………………………………………………………………………………..
…………………………………………………………………………………………………………..
LA PAROLA A…
Alberto Griffini
Channel Manager di GE Intelligent Platforms, Filiale Italiana

GE Intelligent Platforms è la divisione di GE che fornisce le più recenti tecnologie ad elevate prestazioni nell’ambito dell’Automazione Industriale con una vasta gamma di prodotti che vanno dal controllore al sistema di supervisione, offrendo software, hardware, servizi, competenze ed esperienza.
Il ruolo nell’automazione dei tre prodotti. Aree diverse, integrazioni… Le sue considerazioni.
Il PAC ha rappresentato l’evoluzione del PLC verso tecnologia e design tipici del PC. Con il PAC l’hardware e le funzionalità del PLC si sono molto avvicinate al PC industriale. La nostra nuova piattaforma PACSystems RXi utilizza la stessa scheda CPU COMExpress per entrambe le versioni: PC e Controllore, offrendo una soluzione modulare e versatile per applicazioni OEM, RTU e controllo d’impianto produttivo.
Le reti di comunicazioni per questi componenti sono comuni oppure vi sonopunti da evidenziare?
L’aspetto comunicazioni standard in comune è sempre più spinto: ethernet, industrial internet, wi-fi, USB sono chiari esempi di come la tecnologia PC sia ormai diffusa nell’ambito del Controllo Industriale basato su PLC o PAC. La caratteristica di base è ovviamente la robustezza dell’hardware, superiore a quella disponibile nel mercato del Consumer.
Sue considerazioni sul back-up di questi sistemi. Sono richiesti accorgimenti particolari?
A seconda delle richieste di disponibilità del sistema di controllo, quindi di elevati valori di MTBF (Mean Time Between Failure) si possono prevedere soluzioni ridondanti di CPU, comunicazione e ingressi/uscite. Le architetture denominate hot-backup prevedono l’intervento dell’unità secondaria in tempo reale in caso di guasto della primaria, senza creare interruzioni di controllo del sistema e di produzione.
Integrazioni dei sistemi SCADA: particolari considerazioni utilizzando i sistemi indicati.
La classica separazione tra SCADA e Controllore si può dire superata grazie alle nuove soluzioni che utilizzano Soft PLC basati su PC oppure piattaforme integrate di tipo modulare. Questo consente da un lato di ridurre i costi dell’hardware e dall’altro di aumentare le prestazioni in termini di velocità di elaborazione e di raccolta dati. L’utilizzo di CPU multi-core indica la strada verso cui prevedibilmente evolveranno i sistemi di controllo per integrarsi in un unico prodotto.
Controllore PACSystems® RXi. Presenta connettività Gigabit Ethernet ed oltre al design compatto e accattivante e alla possibilità di combinarlo con il modulo IPC della serie, offre un’interfaccia ridondata PROFINET integrata. Con 2 GB di Ram, processore Dual Core su scheda COMExpress, offre elevata connettività
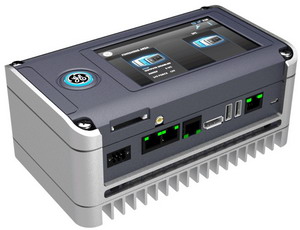
………………………………………………………………………………………………………..
Nicoletta Ghironi
Responsabile Marketing e Comunicazione di B&R Automazione Industriale.
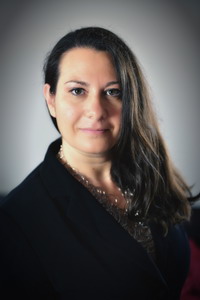
B&R è uno dei riferimenti tecnologici più importanti nella fornitura di sistemi di automazione per costruttori di macchine e sistemi con una proposta completa di soluzioni innovative: controllo, motion, visualizzazione, safety e comunicazione, tutte armonizzate attraverso Automation Studio.
Perchè il design industriale per PC industriali, PLC e PAC è un argomento importante per gli utilizzatori?
Sono tanti gli aspetti su cui l’ingegnerizzazione di un prodotto ha effetto.Un design meccanico ed elettrico a regola d’arte possono fare la differenza in termini di prestazioni operative: robustezza, durata, disponibilità, accessibilità e manutenibilità nel tempo, e di sicurezza e di testabilità del prodotto – una qualità “nascosta” all’utilizzatore, ma che ha effetti sulla diagnostica e sulla garanzia di funzionamento. La combinazione di un buon design con buone tecnologie costruttive permette di soddisfare anche esigenze particolari: l’impiego in ambienti estremi richiede dispositivi con livelli di protezione elevati e range estesi di funzionamento.L’uso in luoghi regolamentati, dove l’igiene dev’essere garantita o ancora dove non si devono accumulare polveri, richiede soluzioni ad hoc, come i pannelli in acciaio inox.con livello di protezione elevato e con superficie frontale perfettamente liscia e igienizzabile.Un ultimo aspetto del design riguarda l’ergonomia, ormai importante anche nell’industria.E di pari passo con l’ergonomia cresce la domanda di personalizzazione dei prodotti, perché aderiscano il più possibile alle specifiche esigenze applicative e costituiscano un tratto distintivo e d’immagine sul proprio mercato.
Il software di sviluppo: una sua analisi sugli sviluppi tecnici.
L’obiettivo è chiaro: ottimizzare lo sviluppo delle applicazioni in modo da ridurre il più possibile gli sforzi e i tempi di realizzazione.Il software del futuro deve venire in aiuto semplificando la vita del progettista e noicon Automation Studio supportiamo queste esigenze.Ad esempio permettendo di usare un unico software per programmare la logica di controllo, il controllo di parti in movimento (motori, robot, CNC), la visualizzazione / interfaccia grafica, oltre che per tutti gli aspetti di progettazione, simulazione, debugging, test e gestione del progetto. In questo modo è sufficiente prendere dimestichezza con un solo strumento di sviluppo e non ci sono problemi di interazione o di compatibilità tra una parte e l’altra.Oltre a comprendere tutti questi aspetti, l’ideale sarà poter portare un’applicazione sviluppata per PLC su un pannello intelligente o su un computer industriale, senza cambiare una sola linea di codice, rendendo possibile un cambio di piattaforma hardware, scalare il sistema in un secondo momento, creare differenti versioni del sistema, senza mai ritoccare il programma.Altra caratteristica indispensabile è la capacità di integrare parti di programma già esistenti, senza doverli riscrivere, riutilizzandoli per progetti futuri, adottando standard industriali per i linguaggi di programmazione, per le comunicazioni e per lo scambio di dati e metadati.L’ultima tendenza è poi quella di offrire al programmatore degli strumenti che lo aiutino a configurare e a creare, in modo grafico e intuitivo, un’applicazione dal nulla. Per tutte le applicazioni più comuni lo strumento di sviluppo semplificherà molto e permetterà, in pochissimo tempo, di avere un’applicazione funzionante.
I costruttori di macchine come vedono i diversi dispositivi di controllo? Alcune loro considerazioni.
Ogni piattaforma è nata per far fronte a esigenze e impieghi differenti ma, con il passare degli anni e lo sviluppo di tecnologie di elaborazione sempre più potenti, robuste e affidabili, le differenze si assottigliano e, pur non evidenziandolo in modo esplicito, molti dispositivi che ancora oggi chiamiamo PLC, sono oggi realizzati con tecnologie embedded che – tolto il fattore di forma fisico (PLC/PAC modulare, pannello, PC industriale) – li rendono, di fatto, tutti dei computer industriali che implementano il controllo in una forma che si è usi definire softPLC.
Dal punto di vista funzionale, di programmabilità e di interfacce, gli stessi dispositivi embedded possono ricadere tranquillamente nella categoria PAC, anche se dal punto di vista del marketing non si sceglie di battezzarli con tale acronimo.Chiarito quindi che, salvo eccezioni che ancora utilizzano tecnologie tradizionali, le moderne piattaforme di controllo sono potenzialmente equiparabili e consentono di realizzare più cicli di controllo paralleli in tempo reale, possono essere programmati in ambienti grafici e con linguaggi IEC standard, sono dotate di interfacce evolute verso i bus di campo standard e possono avere interfacce uomo-macchina evolute, grafiche e remotabili. Le uniche valutazioni che possono aiutare nella scelta, a seconda dell’impiego, sono il formato (peso, dimensioni, attacco), potenza, livello di protezione, livello di integrazione e dotazione di interfacce.
Come vede l’integrazione di questi prodotti a bordo macchina?
Distinguiamo tra interazione delle diverse parti dell’automazione e inserimento dei dispositivi nella struttura fisica della macchina.Il primo punto, l’integrazione logica delle diverse parti del sistema di automazione, è uno degli obiettivi principe di ogni costruttore di automazione.Noi abbiamo riconosciuto l’importanza di una completa e nativa integrazione tra ogni singola parte del controllo, della visualizzazione, della raccolta dati e – oggi più che mai – delle funzioni di sicurezza. Questa capacità di colloquiare di tutte le parti in gioco agevola il programmatore nel suo lavoro. Ogni scambio di dati avviene attraverso i bus di comunicazione, e dato che spesso costituiscono un collo di bottiglia, anche questi assumono un ruolo determinante. Noi, pur offrendo anche la comunicazione con altri bus industriali, abbiamo scelto di adottare Powerlink, un bus di comunicazione real-time ad alte prestazioni, basato su standard Ethernet e tecnologia open-source, per garantire nel tempo la massima apertura e flessibilità. La topologia di connessione e i relativi cablaggi tra i dispositivi hanno un effetto anche sulla parte fisica della macchina: un cablaggio semplice la rende più pulita, ordinata, semplice e veloce da cablare e manutenere, oltre che meno costosa.
Robusto e affidabile, con disponibilità a lungo termine: sono queste le caratteristiche che contraddistinguono l’Automation PC910, il nuovo PC compatto offerto da B&R. La nuova tecnologia Intel® Core™ i di terza
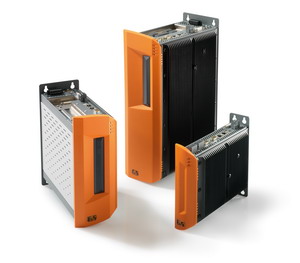
……………………………………………………………………………………………………
Roberto Motta
Local Business Leader IA-Italian Region Rockwell Automation
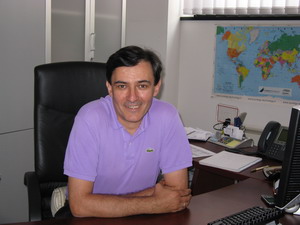
Scelta tecnica di PC industriali, PLC e PAC. Considerazioni in base alla tipologia di Applicazione (processo, macchinario)
Generalmente viene preso in considerazione l’uso di un PAC rispetto a un PLC se l’applicazione richiede:algoritmi di controllo avanzati, modifica estesa dei database, routine di controllo personalizzate integrate, simulazione di processi complessi e necessità di taglie di memoria elevate.Genericamente poi i controllori di automazione programmabili (PAC) sono controlloridi tipo multidisciplinare (processo, discreto, batch, safety e Motion/drive in un unico controllore) e scalabili facilmente integrabili in un’architettura aperta e modulare. I controllori PAC di ultima generazione quali i nostri Logix hanno un sistema operativo multitasking, una struttura della memoria basata su tag, supportano lo stesso set di istruzioni e hanno una struttura logica e linguaggi di programmazione conformi allo standard (IEC 61131-3) attuale.
I vostri clienti sono attenti sulle scelte applicative.Richiedono la vostra consulenza?
Per le applicazioni più complesse è possibile che sia richiesta la nostra consulenza. Le nostre soluzioni di controllo sono altamente integrate e aiutano a risolvere facilmente le sfide legate alla moderna produzione: riduzione dei costi, aumento della produttività, miglioramento della qualità e incremento della flessibilità. I nostri prodotti sono progettati per funzionare insieme, e consentono di ottenere notevoli vantaggi in termini di risparmio di tempo, riduzione dei costi e avvio più rapido.
Considerazioni per gli input/output da utilizzare: a bordo macchina oppure nelquadro elettrico?
Nella scelta rientrano le esigenze di ogni applicazione, i tempi di risposta richiesti, il numero di nodi I/O e loro distanza. Da tempo molte applicazioni quali quelle di controllo di macchine automatiche hanno operato scelte verso un utilizzo largamente diffuso di I/O a bordo macchina. Anche nel caso di I/O in quadro elettrico l’opzione preferenziale è sempre di più quella di I/O studiati per essere applicati originariamente a bordo macchina.Stiamo parlando, nella stragrande maggioranza dei casi, di I/O che vanno ubicati comunque in piccoli quadri di derivazione anche a bordo macchina piuttosto che direttamente con grado di protezione IP67. La larga diffusione di I/O remotati a bordo macchina in armadio è strettamente legata ai tempi di risposta garantiti dalle moderne tecniche di fieldbus, quale p.e. EtherNet/IP in grado di ottimizzare molto più che in passato l’utilizzo della banda di trasmissione della rete.Il numero di nodi I/O e la lunghezza della rete sono gli altri elementi chiave della scelta; con l’aumentare del numero dei nodi, un cablaggio a bordo macchina diviene economicamente vincente, come anche all’aumentare delle distanze il risparmio nella stesura dei cavi I/O diviene più significativo.
Considerazioni sulla diagnostica ed allarmi legata alla scelta del sistema utilizzato. Indicazioni e consigli.
Le informazioni relative ad una diagnostica puntuale stanno divenendo sempre più importanti per ridurre i tempi di fermo macchina o per evitarli del tutto. Una caratteristica molto innovativa resa facilmente disponibile dall’utilizzo della tecnologia TCP/IP anche a livello Fieldbus (p.e. EtherNet/IP) è rappresentata dalla possibilità di gestire informazioni diagnostiche relative anche a semplici nodi I/O utilizzando un generico Internet Browser. P.e. ogni nodo di Rockwell Automation per EtherNet/IP dispone di un’interfaccia web, e da qualsiasi computer, digitando l’indirizzo IP del modulo come URL, i dati relativi al nodo sono visualizzati direttamente su pagine HTML.
I Controllori di automazione programmabili della famiglia Logix sono controllori di tipo multidisciplinare (processo, discreto, batch, safety e Motion/drive in un unico controllore) e scalabili
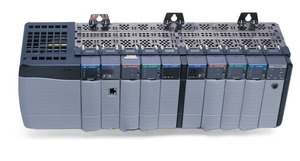
………………………………………………………………………………………………………..
Antonio Marra, Operational Marketing Executive per l’offerta Advanced Motion in Schneider Electric
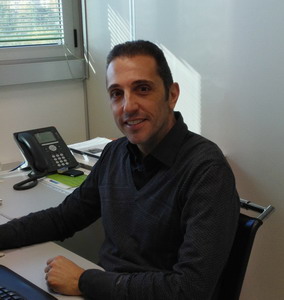
Schneider Electric è lo specialista globale nella gestione dell’energia, offre soluzioni integrate in diversi segmenti di mercato, con una posizione di leadership nei settori energia e infrastrutture, processi industriali, building automation e data center, vantando inoltre un’ampia presenza nelle applicazioni residenziali.
Il mercato dell’automazione ha bisogno di maggior sicurezza informatica. Una sua opinione su argomento.
Lo sviluppo delle reti di comunicazione –tipicamente su base Ethernet- unito alla sempre maggiore integrazione delle tecnologie informatiche a tutti i livelli del processo produttivo, obbliga oggi i fornitori e gli utilizzatori di automazione, a porre una sempre maggiore attenzione al Data Security. Infatti, oggi, per un manutentore di linea è normale collegarsi attraverso un cavo Ethernet a un PC e a un Controller di macchina. Quest’ultimo, essendo sicuramente collegato ad un pannello operatore, apre subito la prima falla verso l’acceso a dati sensibili come le ricette di produzione. Da questo punto in avanti il gioco è semplice. Controller collegati tra loro sulla linea di produzione e linee collegate a strumenti di gestione aziendale aprono la via per l’acceso a dati tipicamente oggi considerati esclusiva del mondo “office”.
? Controllo di processo: verifichiamo un maggior utilizzo di PLC, PC e PAC. Ci saranno nuovi sviluppi?
Sicuramente già oggi il PLC è un attore importante. Per quanto riguarda il PAC o il suo più prossimo parente, il PC, i margini di applicabilità nel futuro saranno sicuramente sempre maggiori. Probabilmente oggi ancora non sono pronti al 100% per sostituire il PLC – in particolar modo nelle applicazioni più tipiche del controllo di processo- ma ritengo che entrambe le soluzioni mettano a disposizione una capacità di calcolo e di configurabilità che sicuramente le farà diventare i principali attori in futuro ormai non lontanissimo.
Gli End User intervengono sulle scelte tecniche di queste soluzioni, oppure delegano gli OEM?
Sicuramente, per quanto riguarda il mondo macchine i grossi End-User influiscono fortemente sulla scelta di alcune tecnologie. Principalmente le prescrizioni sono presenti su tecnologie come PLC, pannelli operatore (HMI), periferiche di campo (I/O). In generale, anche se la tendenza incomincia a cambiare, non esistono ancora pressioni per la scelta dei sistemi come ad esempio il Motion Control. Questi sono ancora “culturalmente” distanti dalle conoscenze degli utilizzatori finali. Ovviamente poi intervengono fattori come la disponibilità dei ricambi, la storicità dei plant (stesso End-User su plant diversi può avere prescrizioni diverse), il livello di conoscenza di determinati sistemi.
Sviluppi futuri dell’automazione degli impianti. Unico hardware potente, centralizzato oppure più sistemi decentrati collegati in rete?
Direi che la tendenza è quella di decentralizzare gli attuatori ma centralizzare l’intelligenza. Ovviamente esistono diversi “livelli” di intelligenza. Se guardiamo ad esempio una linea di produzione, vediamo come questa stia lentamente compattandosi, diventando, dal punto di vista dell’intelligenza, una macchina. La potenza di calcolo dei controllori permette di integrare in un unico dispositivo funzionalità che prima erano distribuite su più unità (es. il numero di servoassi controllati). In questo modo si risparmia in termini di numero di unità di controllo, si eliminano le interfacce di scambio dati, si semplifica il debugging dei SW, si riescono a velocizzare operazioni sincronizzate. Sul lato attuatori invece, la tendenza è esattamente quella contraria. I motivi sono diversi: risparmio nel cablaggio, flessibilità nel realizzare la configurazione, minor spazio occupato dai quadri elettrici. Ovviamente per aumentare questo livello di decentralizzazione il ruolo delle reti di comunicazione diventa fondamentale. Ecco che sistemi basati sulla tecnologia Ethernet, anche se con protocolli diversi, conquistano sempre maggiori spazi.
I controller LMC 101C e 201C completano la serie LMC. Coprono una vasta gamma di applicazioni ed sono in grado di offrire la miglior soluzione con un giusto rapporto fra prezzo e performance, in funzione del numero di assi da sincronizzare, del volume di dati da trasmettere e degli elementi di ro
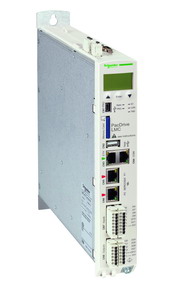